Sixth Custom Rifle
- Howa 1500 Mini Action
- Green Mountain Barrel
- Caliber 221 Fireball
April 2024
In 2018 or 19 I brought home a new Remington 700 ADL Tactical in 223 from the shop for a future project action. Sometime in the years that followed I bought a used Clymer 221 Fireball reamer and started collecting brass. Finally ordered a Green Mountain barrel early in 2024.
I had done some tweaking on my lathe including a new lead screw, half nuts and a cross slide nut. What an amazing difference! It took a lot of backlash out of the system and really made a big difference in performance. Did some additional cleaning and adjusting on the lathe and practiced on some threading procedures including making this little pin for my RCBS Case Master so that I could check case neck thickness on 17 caliber brass.
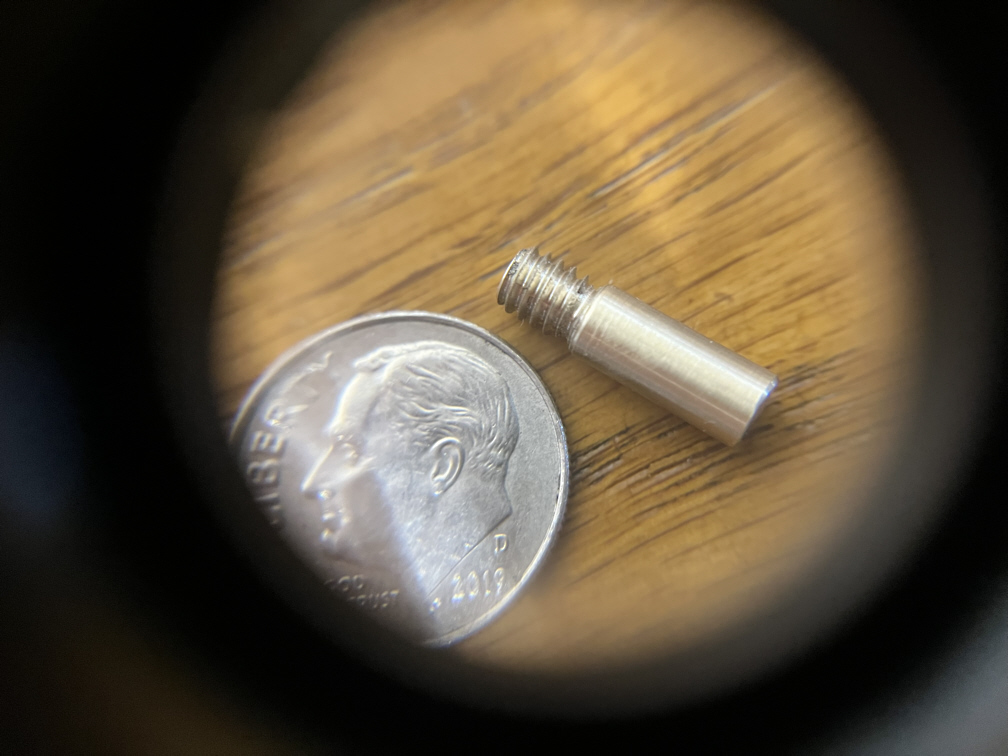
Super small work and very fine thread but it worked out pefectly.
I made the necessary tools to square the face of the Remington receiver and lap the recoil lugs. I practiced creating the bolt nose recess required in the barrel for a Remington action. I had only done this once before and the math alone was driving me crazy. Finally was ready to get started on the new barrel. I intended to make a lightweight barrel to build a coyote hunting rifle in 221. Long story short, was having issues along the way but resolving as I went. When I started chambering the barrel I immediately had chatter in the reamer so I stopped. Tried to determine the problem and could not. So I pulled the barrel off the lathe and put in a practice piece to see if the reamer was the problem. It did not appear to be the problem so back in the lathe with the new barrel but I wasn't taking any chances and reamed the chamber by turning the reamer with a wrench with the lathe turned off. That worked fine. Next step would be threading the barrel tenon and that was going great until the operator made one wrong move that basically ended the Remington project. I turned the wrong handle and destroyed the threading.
Education does not come cheap but I don't have any student loans for you to pay off.
It wasn't a total loss, was just going to have to go a different route. Cutting the threads off and starting over would leave the tenon diameter too small for the Remington action so I purchased a Howa 1500 Mini action barreled in .223.
The Howa action is metric but I have the gears. The plan was to remove the barrel, sell the barrel and use the mini action to create and even lighter coyote rifle. The Howa had other ideas however and the barrel had no intentions of coming off the action without destroying the barrel. So be it, I cut a relief cut just ahead of the receiver and I was then able to remove the barrel.
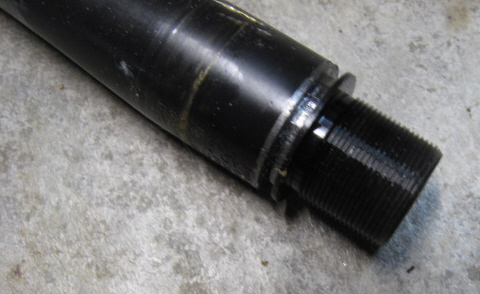
I made the tools to square the Howa receiver face and lap the recoil lugs. One lug was not making contact at all. So that work was completed before starting on the barrel because it does change dimensions slightly. The Howa uses the same style bolt nose recess and I had the old barrel handy for reference to make sure my numbers made sense. I wanted the tolerances tighter than the factory barrel and was able to accomplish that.
Somewhere along the way I discovered that I had not adjusted the Gibs on my cross slide properly and that had lead to some of the issues I had been having. That was corrected and the rest of the project went pretty smoothly. It is interesting and educational to make mistakes. I am understanding the lathe more all the time and can recognize or figure out what's going on. Thanks to books and youtube videos, I am gaining on it.
Prior to starting all this mess, I had practiced threading the muzzle end of an old barrel so that when the time came I could thread the 221. I was now to that point so I gritted my teeth and went for broke. The threads did not turn out pretty but they work. I put an 11 degree crown on the barrel and then went to work on making a thread protector from a piece of aluminum bar stock and then on an actual barrel scrap. I had never done internal threads so back to the books and videos. The barrel was threaded 1/2x28 so the protector would require a tool bit for threading without the use of a boring bar. Sure, I could buy a thread protector in any style or flavor you can think of but why would I? If I can thread a tenon and chamber a barrel why do I need someone elses thread protector. I did not have any high speed steel blanks to grind a tool bit out of so I asked in the Atlas facebook group if I could make a bit out of one of the many hole reamers that I had been given years ago. It was confirmed that the reamers are high speed steel but as expected I was told that would be a waste of a good reamer and that I should just buy the tool bit. So I dug farther in the dark corners of my cabinets and found some wicked hard looking lathe tool bits. Fired up the grinder and started making sparks. It didn't take too long before the tool began to take shape. I drilled a hole in the aluminum bar stock and set out to cut some threads. It took a few attempts to make it turn out right before I attempted to use the barrel scrap. But all went pretty well and the protector turned out nice.
I test fired the rifle and lived to tell about it so I ordered a lightweight stock from Boyd's and it was a simple drop in as usual. Love the Boyd's stocks.
The finish on the actual barrel turned out rougher than I had hoped because of the Gib adjustment issue but I had intended to paint it or cerakote it anyway. A friend of mine told me he knew a guy that could powder coat it for me at a reasonable price but before I spent another dime on this project I wanted to run the barrel through the break-in procedure and make sure it had potential to shoot well. So on 4/6/24 I loaded up a handfull of rounds and headed down to my shooting bench. Just put together rounds with 40 grain bullets pushed by the book start charge and everything went well. The 221 round will actually feed from the magazine and eject. It has potential for sure so on 4/9 I dropped the barrel off to have it powder coated. Picked it up on 4/11, that's pretty fast. Turned out pretty sharp and should be durable.
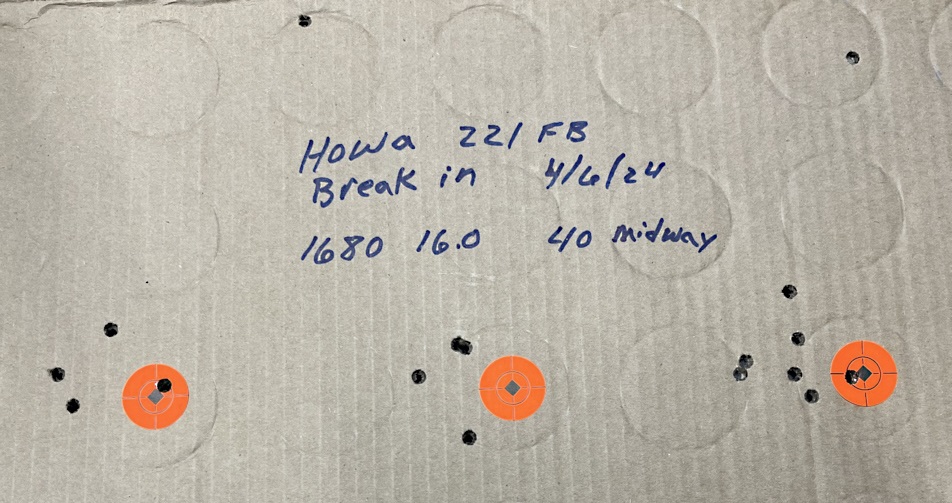
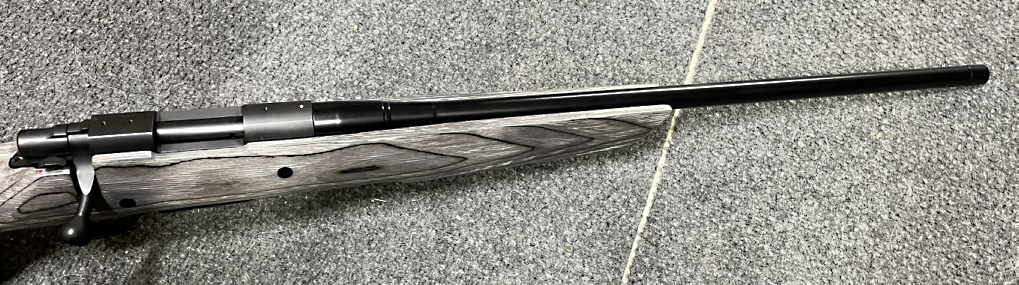
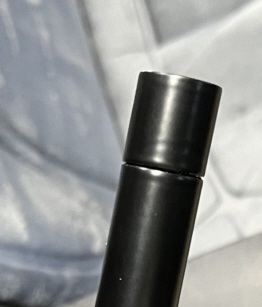
Epoxy bedded it on 4/20 and that worked well once again but it's always a scary operation.
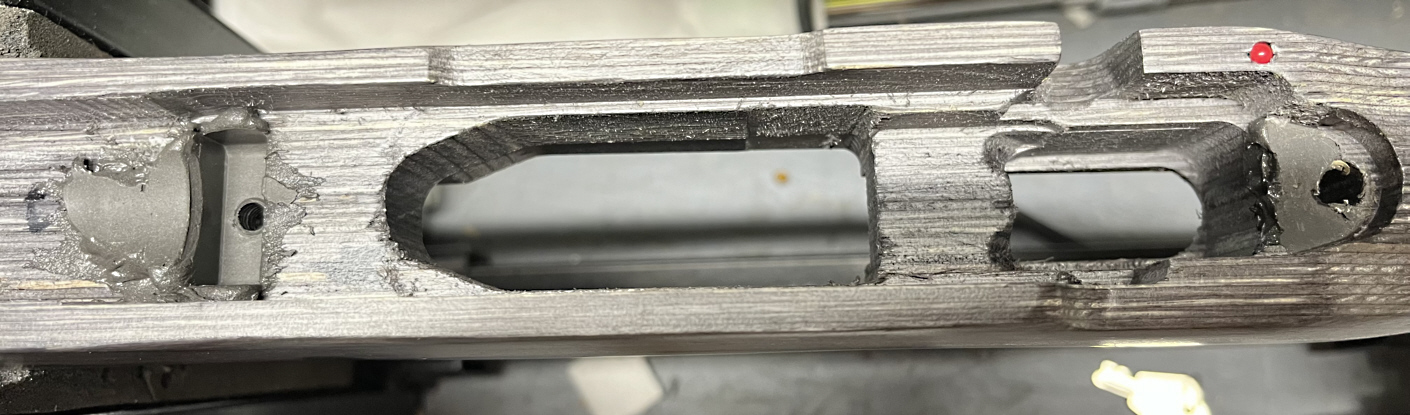
Loaded up 4 different loads to test on 4/21 and the winner so far was the last group. I knew I pulled the top right bullet before I found the shot on the target. This load had way more bullet jump than what I usually work with but it does show me potential anyway.
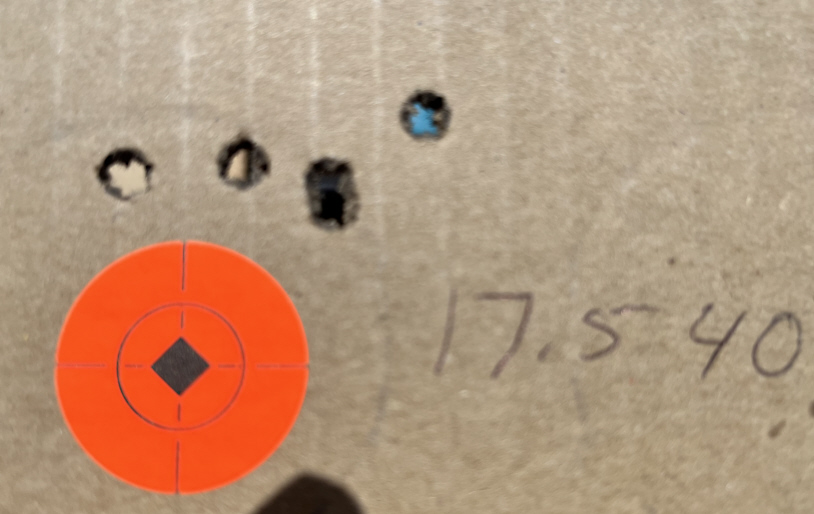
Update October 2024
I played with a couple more loads late in June but nothing amazing. Tried RL7 powder the first part of October and found a keeper. Ironically this can of powder is 40 years old.
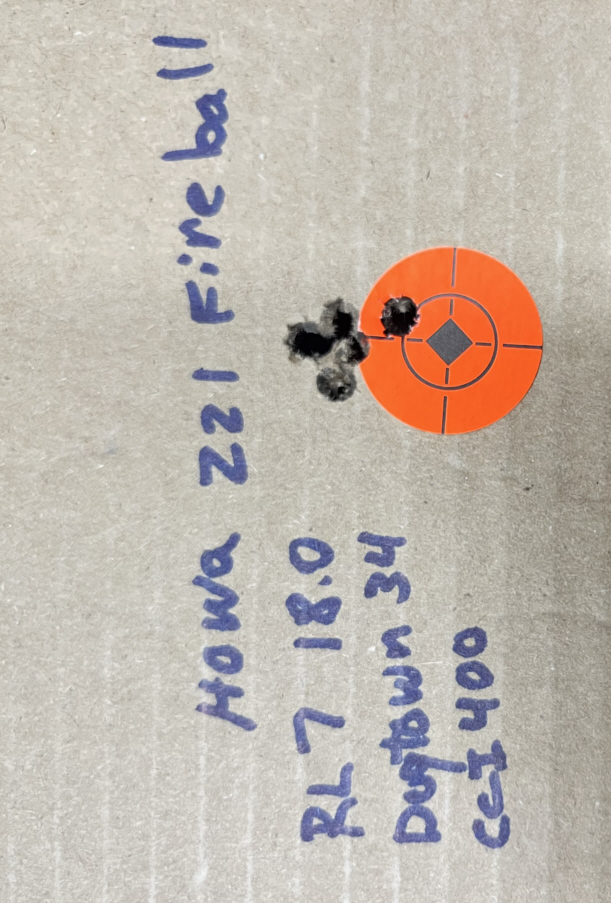
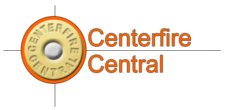